Service Information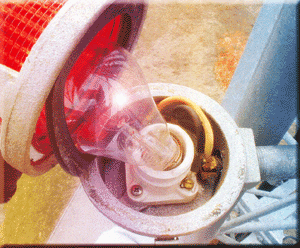
Lighting Systems Maintenance
The installation and maintenance of lighting systems is a specialty that many companies advertise, but sometimes find that their technicians are not as knowledgeable as they should be with tower lighting components.
Lighting maintenance can be one of the tower site’s most expensive items in the owner’s budget, regularly exceeding property taxes and insurance for some locations.
A preventative maintenance program can ensure lower overall lighting maintenance costs, but a number of tower owners try to minimize their expenses by only servicing the lighting equipment when there is a reported failure.
When selecting a lighting maintenance contractor, ensure that they are qualified to work on the installed system. Some lighting repair services will warranty their
work for a period of time and also stock many spare components so that a costly return trip is not required. A number of monitoring systems will troubleshoot the lighting system and identify what component level has failed prior to the contractor mobilizing.
Technical training and certification classes are available through most lighting manufacturers. High intensity lighting installations and repairs require a greater degree of experience and product knowledge.
A fully trained service technician might cost the tower owner slightly more for repairs, but the value added services they provide through their competency is offset by their quick and professional repair. It is advisable to check with the manufacturer to identify that the firm you are using will be approved for handling any warranty issues.
It is the FAA’s position that aviation obstruction lighting systems that have been serviced using non-original equipment manufacturers' parts are no longer in compliance with FAA specifications of FCC regulations. For further information see Policy Letter on Non-OEM Components.
Bulb failure is the most common occurrence. The lamp, without any markup by the contractor, can cost as little as $35.00 for a 600W bulb to $450.00 for a flash tube. Contracts are let on an individual project basis or an ongoing flat rate agreement. Hourly man-hour pricing averages between $60.00 and $80.00. Although many service calls will require only one technician, if the repair is required to be made on the tower, two employees must be on site to comply with OSHA requirements. Some companies will provide repairs for $450.00 per visit plus parts, based upon receiving multiple sites at one time. However, at this pricing, seldom will there be any value added services provided by the contractor, preventative maintenance that could avert another repair call. If a lump sum price is used there should be a clear understanding of return trip responsibilities, parts being supplied, tall tower differentials and extended travel outside of a given geographic area.
Convince your customer to only use bulbs that are known for their quality, longevity and industry acceptance. Trying to save a few dollars on the lamping product is foolish if it requires the installation contractor to make an unanticipated return trip to replace it.
We recommend that you contact our valued tower lighting maintenance and installation contractors to obtain additional information about their services, capabilities and experience.
Help for premature bulb failures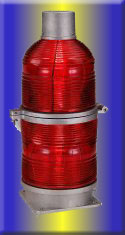
If the lighting system has been having premature bulb failures, check the voltage at the bulb itself and ensure that the seals around the lenses are in good shape. Sometimes frequent bulb failures can be caused by power spikes. Have the utility company monitor the line voltage for power.
Check leads before climbing
Seasononed technicians will isolate the beacon that is not working and remove the hot lead from the controller. They'll check this lead to the ground and to the neutral. If the bulbs are blown they should read an open to neutral and an open to ground. If the beacon reads a short to either neutral, ground or both, chances are the problem is more than a failed bulb.
Don’t wait until the 14th day to call a contractor
Tower owners are required to report to the FAA a known lighting outage that cannot be repaired within 30 minutes if it affects a top height or flashing obstruction light regardless of its position so that a Notice to Airmen (NOTAM) can be issued. Failure of a steady burning side or intermediate light should be corrected as soon as possible, but notification is not required. Once the NOTAM is provided the owner has 15 days to make the repair.
FCC violations for failure to report outages range from $10,000 for outage of a singe light to $15,000 for failure to display all obstruction lights. When there are serious violations the Federal Commission can double the fines. One tower owner was recently fined $90,000 for multiple violations.
Under Section 17.47 of the FAA’s rules, the owner of any antenna structure registered with the Commission and assigned lighting specifications must (a) check antenna lights once every 24 hours by observing the lights or properly maintained indicators, or by maintaining an alarm system designed to detect light outages, and (b) thoroughly inspect all control devices, indicators and alarm systems associated with antenna lights at least once every 3 months.
In addition, Section 17.48 requires that owners of such structures immediately report any antenna light outage not remedied within 30 minutes to the nearest FAA Flight Service Station or office. Light outages that cannot be repaired within 15 days must be re-reported to the appropriate FAA Flight Service Station. The FAA Flight Service Station must also be notified once repairs are complete.
Under the reporting procedure, the FAA Flight Service Station requires that the seven-digit Antenna Structure Registration Number (commonly referred to as the "ASR number" or "tower number") be provided when information about the status of a light outage is conveyed to FAA personnel. In addition, Section 17.48 requires that the FAA be informed of the condition of the light or lights, the circumstances that caused the light failure, the probable date for restoration of service, the height of the structure (AGL and AMSL if known), and the name, address, and telephone number of the person reporting the outage.
|