North Carolina Communications Tower Standard 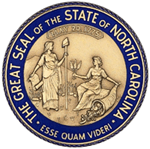
13 NCAC 7F.0600
CHAPTER 7 - OFFICE OF OCCUPATIONAL SAFETY AND HEALTH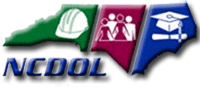
SUBCHAPTER 07F - STANDARDS
SECTION .0600 – COMMUNICATION TOWER STANDARDS
13 NCAC 07F .0601 SCOPE AND APPLICATION
(a) The rules in this Section contain requirements for policies, procedures, and safe work practices to protect employees throughout North Carolina from the hazards of working on communication towers during construction, alteration, repair, operation, inspection, and maintenance activities.
(b) A communication tower is defined as any tower over six feet in height that is used primarily as an antenna or to host one or more antennas. Where the communication tower is affixed to another structure, such as an electrical transmission tower, church steeple, building rooftop, or water tower, the applicable part of any controlling regulation for protection of employees (e.g., 29 CFR 1910.268, 29 CFR 1910.269 and 29 CFR 1926 Subpart V for transmission towers) shall apply up to the point of access to the communication tower. Thereafter, the provisions of this Section shall apply.
(c) The rules in this Section shall not apply to communication towers that are mounted on motor vehicles.
History Note: Authority G.S. 95-131;
Eff. February 1, 2005.
13 NCAC 07F .0602 DEFINITIONS
In addition to the definitions set forth in 29 CFR Part 1910 and 29 CFR Part 1926, the following definitions apply throughout the rules in this Section:
(1) Acceptable Conditions for Access mean the conditions that must exist before the employer grants permission for construction, alteration, repair or maintenance work to be performed on a communication tower. These conditions include the following:
(a) Work under the control of a work safety program meeting the requirements of the Rules in this Section; and,
(b) Work where an accumulation of snow, ice or other slippery material is not present, except as necessary for the inspection or removal of such material;
(c) Notwithstanding the prohibitions outlined in Sub-item (1)(b) of this Rule, if tower emergency maintenance work must be performed where there is an accumulation of snow, ice or other slippery material, the employer shall implement safe work practices (equipment, practices and procedures) that address the hazards known to be associated with tower work to minimize the associated risk to employees while working on the tower structure and the support structure to which it is affixed, where applicable.
(2) Climbing Facility means a component specifically designed or provided to permit access to the tower structure, such as a fixed ladder, step bolt, or other structural member.
(3) Competent Person means a person who is trained to identify existing and predictable hazards in the surroundings or working conditions that are hazardous or dangerous to employees, and who has authorization from his employer to take prompt corrective measures to eliminate them, including halting the work as required by the rules in this Section.
(4) Elevated (High Angle) Rescue means the process by which methods and equipment are utilized in order to gain access to and egress from the location of an injured employee(s) on the tower structure, and lower both the injured employee(s) and the rescuer(s) to the ground safely.
(5) Fall Protection Equipment means the personal equipment that employees utilize in conjunction with 100% fall protection systems, including connectors, body belts or body harnesses, lanyards and deceleration devices.
(6) Ladder Safety System means an assembly of components whose function is to arrest the fall of a user, including the carrier and its associated attachment elements (e.g., brackets, fasteners), the safety sleeve, and the body support and connectors, wherein the carrier is permanently attached to the climbing face of the ladder or immediately adjacent to the structure.
(7) One-Hundred Percent (100%) Fall Protection means each employee exposed to fall hazards above six (6) feet while ascending, descending, or moving point to point, must be protected by fall protection, as described in 13 NCAC 07F .0606(c), at all times.
(8) Qualified Climber means a person who has, by virtue of knowledge, training, and experience, been deemed qualified in writing by his employer to perform tower work.
(9) Qualified Person means a person possessing a degree, certificate, professional standing, or knowledge, training, and experience in the field of communication tower work, and who has demonstrated to his employer his ability to resolve problems relating to the subject matter, the work, or the project.
(10) Safety Sleeve means the part of a ladder safety system consisting of the moving component with locking mechanism that travels on the carrier and makes the connection between the carrier and the body support.
(11) Site means the communication tower and the surrounding land or property where tower work is being performed.
(12) Step Bolt means a bolt or rung attached at intervals along a structural member and used for foot placement during climbing or standing.
(13) Tower Construction means the building of a new tower or structure, or the installation of new equipment on an existing tower or structure.
(14) Tower Emergency Maintenance Work means the repair, restoration or replacement of any pre-existing device installed on the tower in the interest of public safety, such as, aviation signaling devices and equipment used to transmit or receive broadcast signals.
(15) Tower Inspection means the procedure in which an employee(s) climb(s) or ride(s) the structure’s elevator to visually inspect the tower for potential problems, and test for tower plumbness and guy cable tension.
(16) Tower Maintenance Work means the replacement in kind of any device on an existing tower, the repair of existing equipment, and painting.
History Note: Authority G.S. 95-131;
Eff. February 1, 2005.
13 NCAC 07F .0603 EMPLOYER RESPONSIBILITIES
(a) The employer shall require employees to adhere to acceptable conditions for access, as defined by 13 NCAC 07F .0602(1), prior to climbing the tower at heights above six feet.
(b) The employer shall ensure that at least two employees, including at least one competent person, are on site at all times when employees are exposed to fall hazards above six feet, provided however, an employer shall not be required to have more than two employees on site at any given time.
(c) A competent person shall visually inspect the tower base for damage, deterioration, structural deficiencies and functionality of safety features and anchorages before employees are allowed to climb the tower at heights above six feet. Additionally, the employer shall ensure that the tower is visually inspected for these items, as it is ascended, to the elevation point where work is being performed.
History Note: Authority G.S. 95-131;
Eff. February 1, 2005.
13 NCAC 07F .0604 HAZARD IDENTIFICATION AND ASSESSMENT
(a) In addition to the inspections required by 13 NCAC 07F .0603(c) and 13 NCAC 07F .0605(b), the employer shall conduct a hazard assessment to identify, assess, and control employee exposure to hazards as required by the rules in this Section and any other applicable state or federal statutes, rules or regulations.
(b) The employer shall perform and document the hazard assessments required by this Rule:
(1) Initially and daily for each site prior to permitting employees to climb the structure; and
(2) When safety and health information or change in workplace conditions indicates that a new or increased hazard may be present.
(c) The hazard assessments required by this Rule shall:
(1) Be performed by a competent person;
(2) Evaluate new equipment, materials, and processes for hazards before they are introduced into the workplace; and
(3) Identify meteorological conditions that could affect work at heights above six feet on a tower, such as wind, rain, snow or ice.
(d) If hazards are identified, the employer shall assess the severity of identified hazards and implement means to control such hazards, including providing employees with personal protective equipment (PPE) designed to control the identified hazards and ensuring the proper use of the PPE by the employees.
History Note: Authority G.S. 95-131;
Eff. February 1, 2005.
13 NCAC 07F .0607 HOISTS AND GIN POLES
(a) Hoists. Hoists used during the construction, alteration, repair, maintenance, or demolition of communication towers shall meet the following requirements:
(1) All hoists shall meet the requirements set forth in this rule, 29 CFR 1910, Subpart N, and 29 CFR 1926, Subpart N, where applicable.
(2) All hoists shall meet applicable requirements for design, construction, installation, testing, inspection, maintenance, and operation as prescribed by the manufacturer, or a licensed professional engineer.
(3) Employers shall maintain at the work site the operating manual developed by the manufacturer for the specific make and model hoist being used, as well as documentation for any inspection, testing, and operator training certification required by the rules in this Section,
(4) An employer shall not operate or permit to be operated a hoist that the employer knows, or reasonably should know, will expose his employee(s) to an unsafe condition which is likely to result in personal injury or property damage.
(b) Gin Poles.
(1) Rigging Equipment.
(A) Wire rope, slings, chains, shackles, turnbuckles, links, hooks, sheaves,
rotating rooster heads, blocks, and hoists, used in a gin pole lifting arrangement shall meet the manufacturer's safe working load limits. In addition, each component shall have a nominal breaking strength of no less than five times the static load applied. Consideration for end fitting losses and actual positioning of connecting parts shall
be given;
(B) Lugs or other devices for lifting or attaching the gin pole in position shall
be designed with load and resistance factors appropriate for their intended use;
(C) Only alloy chains marked by the manufacturer with an 8, T, or an A, rated for lifting, shall be used;
(D) Only quenched and tempered hooks and shackles shall be used. The
manufacturer's load rating shall be stamped on the product; and (E) The breaking strength of the sheave shall equal or exceed the breaking strength of the wire rope intended for the sheave.
(2) Gin Pole Use.
(A) A user's gin pole load chart shall be provided for each pole;
(B) Any special engineered pick, which is outside of the load chart, shall only beallowed at the direction of a licensed professional engineer. Monitoring and measuring conditions, as specified by a licensed professional engineer, shall be provided and used during all special engineered picks;
(C) Modifications or repairs of a gin pole shall be made with like or similar
materials to meet or exceed the original specifications. Modifications or repairs shall be recertified by a licensed professional engineer; and
(D) There shall be a mechanism in place to prevent the gin pole from tipping during the jumping process.
(3) Wire Rope. Wire rope used for rigging shall be as follows:
(A) Compatible with the sheaves of the rooster head and hoisting blocks;
(B) Lubricated in accordance to manufacturer specifications to prevent corrosion and wear;
(C) End connections shall be terminated per industry and manufacturer's
specifications;
(D) Wedge sockets shall have a minimum tail length of one rope lay with a
properly torqued clip attached to prevent accidental disengagement; and
(E) Flemish eyes shall contain heavy duty thimbles of appropriate size for the
wire rope diameter, and shall have a minimum tail length of one rope lay secured with a properly torqued clip at its end.
(4) Inspections.
(A) Gin poles shall have a documented inspection annually by a qualified person;
(B) In addition to the annual inspection, the employer shall designate a
competent person who shall visually inspect the gin pole and rigging prior to each use, and during use, to make sure it is in safe operating condition. Any deficiencies shall be repaired before use continues;
(C) During each inspection, the qualified or competent person shall inspect the
legs and bracing members for bends or distortion;
(D) During each inspection, the qualified or competent person shall inspect the
straightness tolerances for the overall assembly (including leg and bracing members);
(E) During each inspection, the qualified or competent person shall visually
inspect the welds for quality, deformation, cracks, rust, or pitting or loss of cross sectional area;
(F) During each inspection, the qualified or competent person shall inspect the
members for excessive rust or pitting or loss of cross sectional area;
(G) During each inspection, the qualified or competent person shall inspect the
sling attachment points for distortion, wear, cracks, and rust;
(H) During each inspection, the qualified or competent person shall ensure that
proper bolts are utilized and all associated hardware is in good condition;
(I) During each inspection, the qualified or competent person shall inspect side
plates on rooster heads for distortion or other damage;
(J) During each inspection, the qualified or competent person shall inspect all
attachment hardware, including rigging and parts such as cables, slings, and sling attachment points, shackles, hooks, and sockets for wear, distortion, cracks, and rust; and
(K) During each inspection, the qualified or competent person shall ensure that
all problems identified during the inspection are corrected before placing the gin pole into service.

History Note: Authority G.S. 95-131;
Eff. April 1, 2005.
13 NCAC 07F .0608 RECORDKEEPING
In order to fulfill responsibilities under the provisions of the rules in this Section, the employer shall, upon request, provide the Deputy Commissioner of Labor for Occupational Safety and Health or his designee access to the following records:
(1) Training Records. All material related to the employer’s training and education program, pursuant to 13 NCAC 07F .0609.
(2) Medical Records and Non-Ionizing Radiation Exposure Records. All medical records (in accordance to 29 CFR 1910.1020(d)(1)(i)) and material related to each analysis using exposure or medical records (in accordance with 29 CFR 1910.1020(d)(1)(iii).
(3) Equipment Inspections and Testing Records. All material related to the modification, repair, test, calibration or maintenance service of all equipment.
History Note: Authority G.S. 95-131;
Eff. February 1, 2005.
13 NCAC 07F .0609 TRAINING
(a) In order for employees to work at heights above six feet on a communication tower, they must be approved for such work by a qualified person.
(b) Competency of the Trainer. Training of employees in communication tower work shall be performed by or under the supervision of a qualified person.
(c) Written Work Procedures.
(1) The employer's written work procedures shall be provided to employees as part of their training.
(2) Pictures and symbols may be used as a means of instruction if employee understanding is improved using this method.
(3) Manufacturers' operating manuals for personnel hoisting systems satisfy the requirement for operating procedures for the respective equipment, or can serve as the basis for these procedures.
(d) Hazardous Materials Training. Employees required to handle or use flammable liquids, gases, or toxic materials shall be instructed in the safe handling and use of these materials and made aware of the specific requirements contained in 29 CFR 1926.55 and 29 CFR 1910.1200, as applicable.
(e) Fall Protection Training.
(1) The employer shall provide a training program for each employee who might be exposed to fall hazards.
(2) The program shall enable each employee to recognize the hazards of falling and shall train each employee in the procedures to be followed in order to minimize these hazards.
(3) The employer shall ensure that each employee has been trained by or under the supervision of a qualified person in the following areas:
(A) The nature of fall hazards in the work area;
(B) The correct procedures for erecting, maintaining, disassembling, and inspecting the fall protection systems to be used;
(C) The correct procedures for inspecting fall protection equipment for wear, damage, defect or deterioration.
(D) Climbing safety procedures;
(E) The use and operation of the fall protection systems utilized by the employer, as described in 13 NCAC 07F .0605(c);
(F) The role of each employee in any safety monitoring system being used;
(G) The correct procedures for the handling and storage of equipment and materials and the erection of overhead protection;
(H) The role of employees in fall protection plans; and
(I) The compatibility of fall protection equipment and fall protection systems.
(f) Hoist Operator Training. The employer shall maintain documentation that the hoist operator has practical training on the hoist he is operating. Training of hoist operators shall meet the requirements of 29 CFR 1910.179 and 29 CFR 1926, Subpart N.
(g) RF Training.
(1) All employees exposed in excess of the general population/uncontrolled MPE limits stated in 47 CFR 1.1310 shall receive RF hazard awareness training by or under the supervision of a qualified person in the following areas:
(A) MPE Limits for occupational/controlled exposure;
(B) Recognition of RF exposure sources in communication tower work;
(C) Proper use and interpretation of RF exposure;
(D) Work procedures to avoid excessive RF exposure;
(E) Proper use of RF protective clothing and other related PPE;
(F) Symptoms and health issues related to RF exposure; and,
(G) RF exposure first-aid procedures.
(2) Employers shall ensure that each affected employee who works in an electromagnetic energy environment with potential RF exposure in excess of the general population/uncontrolled MPE limits stated in 47 CFR 1.1310 has access to and understands the specific site information related to the RF energy and RF fields present at each individual site.
(h) Retraining. Unless stated otherwise in this Rule, when the employer or qualified person has reason to believe that any employee who has already been trained does not have the understanding and skill required to safely perform the work assigned, the employer shall retrain each such employee. Circumstances where retraining is required include situations where:
(1) Changes in the workplace render previous training obsolete;
(2) Changes in the types of fall protection systems or equipment to be used render previous training obsolete; or
(3) Inadequacies in an employee's knowledge or use of fall protection systems or equipment indicate that the employee has not retained the requisite understanding or skill.
(i) Training Records.
(1) The employer shall certify that each employee has been trained by preparing a certification record which includes:
(A) The identity of the person trained;
(B) The signature of the employer or the qualified person who conducted the training; and
(C) The date that training was completed.
(2) A copy of the training lesson plan for each topic of instruction shall be maintained by the employer.
(3) The certification record shall be prepared at the completion of the training required by this Rule and shall be maintained for the duration of the employee's employment.
(4) The most current certification record shall be kept available for review by the Deputy Commissioner of Labor for Occupational Safety and Health or his designee, upon request.
(5) An employer may accept training records or certificates for previous training if the employer verifies that all training and knowledge is current and applicable to the new employee's job duties.
History Note: Authority G.S. 95-131;
Eff. February 1, 2005.
|