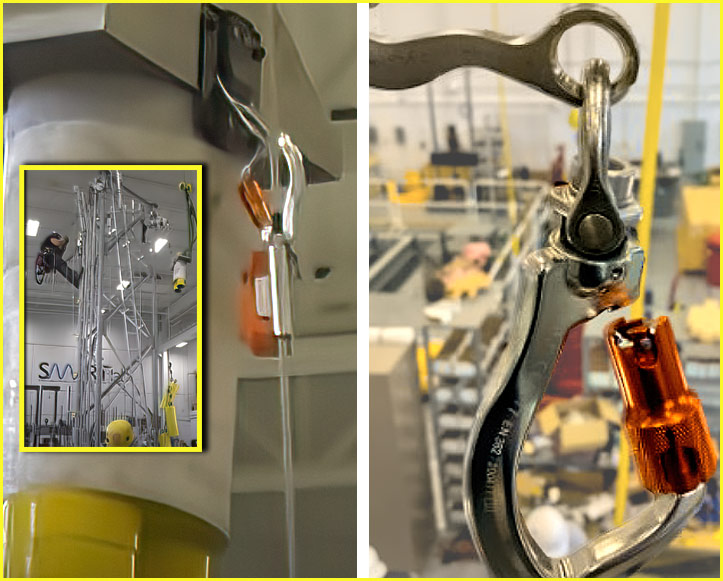
A SERIOUS TESTING FAILURE was observed by the Safety Equipment Manufacturers Committee when a wire sleeve’s carabiner connecting device’s gate sheared, and the sleeve became detached from the D-ring attached to a test torso. The failure occurred (inset photo) during a test when a fall occurs with the static weight of three additional climbers. The drop scenario was designed to replicate the fourth climber falling above the additional static load of three climbers on the wire rope safety climb system. The failure can be seen at 1:42 in the video.
NATE: The Communications Infrastructure Contractors Association unveiled a video highlighting the safety sleeves testing events held by the Safety Equipment Manufacturers Committee (SEMC) at the University of Dayton Research Institute in Dayton, Ohio.
The video conducts a deep dive into the SEMC’s protocols and procedures that were implemented to test safety sleeves by replicating how they are utilized by technicians in the field at tower sites.
Although it is not discussed in the video, at 1:42, a severe sleeve failure can be observed during a test drop, which would have likely ended in a climber fatality. It appears that the carabiner connecting device’s gate was sheared and became detached from the D-ring attached to a test torso.
All manufacturers of wire rope safety climb sleeves have a total rated capacity of 310 lbs., including worker weight and tools. Therefore, SEMC’s testing was completed to match the full rated capacity of the sleeve.
In the United States, all required ANSI tests for wire rope safety sleeves are performed from a static starting position, utilizing a cylindrical 282 lb. test weight at a specified stand-off distance from the wire rope.
However, SEMC elected to utilize a heavier test torso to replicate real-world scenarios better, including the climber’s movement, motion, placement on the system, and center of gravity.
“This video does a great job of breaking down the comprehensive nature and the technical steps involved in the SEMC’s safety sleeve testing initiative,” said committee member Joey Deuer, President of Deuer Development.
Deuer informed Wireless Estimator that ANSI Z359 Standard isn’t robust enough in terms of simulating real-life conditions and that additional testing criteria should be considered by ANSI.
He believes that the new standard, expected next year, will incorporate a number of SEMC’s recommendations and testing criteria.
The Miller Vi-Go (SW) that failed in the video was compliant with the ANSI Z359 standard. Still, its failure personifies SEMC’s belief that additional testing will provide safer equipment that is tested under real-world conditions.
Deuer emphasized that the work that NATE’s SEMC has performed will benefit the country’s professionals who work at heights, not just communications workers.
The group tested safety sleeve performance on corroded cables, painted cables, cables with parasitic ice, improperly tensioned cables, cables at different angles, and other real-world scenarios. In round one of the testing event, 110 drop tests were conducted over a period of six days. In round two of the testing, 45 drop tests were conducted over three days.
SEMC is cautioning climbers not to leave unattended or non-secured wire rope safety sleeves attached to the wire rope safety climb.
Also, the user should verify that the wire rope safety sleeve meets and is utilized per the manufacturer’s specification and is compatible with the wire rope safety climb to be used, including the wire rope diameter and construction.
According to Deuer, the biggest takeaway from the testing was that properly tensioned cable is critical to the function of the system. If you do not have tension on the wire rope, some sleeves will not function and may fail.