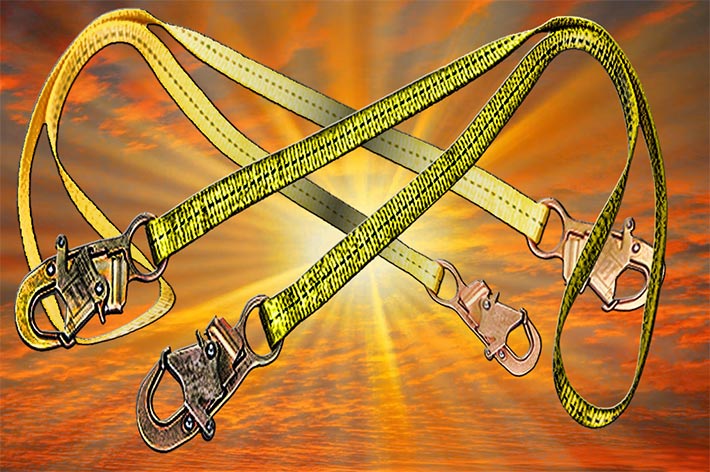
Roughly 41% of the total average strength loss of webbing was attributed to UV radiation
Equipment exposed to the environment can have an effect on technician safety, effective use, and longevity. The focus of this Planning Advisory Notice (PAN), published with permission by the Telecommunications Industry Foundation, is: Best safety practices for slings, ropes, harnesses, and hard hats to help technicians identify and prevent environmental exposure and ultraviolet degradation.
In 2017, Brigham Young University conducted a study on webbing strength loss, “Long-Duration Environmental and Blood Effects on Webbing Strength Degradation.” The methodology of the study was simple, they took 6’ sections of nylon webbing and hung them outside for one year in seven separate climates and elevations across North America. Some of the chosen locations were Arapahoe Basin Ski Resort in Colorado, Bishop, California, and Anchorage, Alaska. Two control samples were stored in a climate-controlled environment away from direct sunlight in Columbus, Ohio. At the end of the year, all samples were returned and subjected to a uniform strength test.
In just one year webbing exposed to the elements had an average strength loss of 27.7%
The result of the test determined webbing exposed to the elements for one year led to an average strength loss of 27.7%. As a reminder, this equipment was not used for its intended purpose but simply exposed to the elements. Zero percent of this strength loss was due to any usage factors. Additionally, safety harness webbing, rope, and slings are typically comprised of nylon, polyester, or a combination of the two. Since these materials will experience comparable degradation from exposure to wind, temperature, precipitation, and UV radiation, we are able to use this study to provide guidance for equipment subjected to these types of environmental exposure.
Wind, temperature, and precipitation combined for roughly 51% of the total average strength loss from the study. Barring a significant weather event, wind itself is not a strong factor in the degradation of nylon webbing. However, wind does open the potential for airborne particles and dirt to attach to equipment and the opportunity for slings and rope to repeatedly impact the structure or surface that it is attached. This impact abrasion can lead to signs of wear, fraying, breaks, loosened/pulled threads, or cuts.
The impact of temperature on webbing strength is theorized to be relatively minimal (barring high extremes that will burn or glaze) but it is still important to take precautions. Inspection must be conducted to identify glazing, discoloration, or hard/soft sections. Rain and other precipitation also did not significantly degrade the rope compared to other sources. Though, climates with high airborne salt content could cause damage to harness hardware or rope terminations. It is important to inspect buckles, attachment points, and hardware for proper function and for signs of corrosion, pitting, rust, cracks, or breaks.
Roughly 41% of the total average strength loss was attributed to UV radiation. The most notable negative impacts of UV radiation included the loss of tensile strength, loss of flexibility, and decreased elasticity. These findings were confirmed by the lesser degradation of samples in Canada and Alaska due to the shallower angle of the sun for many parts of the year. Further, large portions of the day in these areas would have cast the webbing in the shade. Fortunately, UV degradation is relatively easy to identify. Inspect for significant fading, stiffness, lack of pliability, or a fuzzy texture along the length of webbing or rope.
About 5.5% of the total strength loss was attributed to the age of the nylon webbing. This places emphasis on tracking the date of manufacture and inspecting and documenting the date equipment is put into service. If the equipment is not marked with a date of manufacture, it becomes impossible to know the age of the product unless there is a log of when it was put into service. For additional information, see OSHA’s Guidance on safe sling usage.
Breaking strength of a nylon sling sees an overall 27.7% loss
To put all of these strength losses in context, consider a nylon webbing sling with a breaking strength of 5,000 lbs. Over the course of this study, this sling will have experienced an average of 27.7% overall strength degradation, reducing its breaking strength to 3,615 lbs. (loss of 1,385 lbs.). Contributors to the loss are wind, temperature, and precipitation will be responsible for 710 lbs. of strength loss, UV radiation 567.5 lbs., age 75 lbs., and some minor miscellaneous factors 32.5 lbs.
Even though this study included seven varied outdoor climates, it is important to remember that these studies cannot fully replicate the impacts of utilizing a sling, rope, or PPE while working on a tower. While compiling research for this article we received an anecdotal account from a tower technician. His crew left a temporary lifeline up overnight and pulled the rope down to inspect in the morning. They discovered the lifeline was nearly sheared in half by the wind rubbing the temporary lifeline against steel overnight. If they had not been trained and had not thoroughly inspected the rope, they could have easily assumed everything was alright and experienced serious consequences.
Proper care and maintenance will serve to mitigate the impacts of environmental exposure. Harnesses, slings, and rope should be stored loosely and packed in a clean, dry environment. Wet equipment should be thoroughly dried before storage and never dried in a heated dryer. Keep gear away from exposure to direct flame or high temperatures, such as in a hot car or long-term storage in an outdoor storage bin. Environmental exposure will impact the estimated life span of all equipment but taking these precautions can help get gear closer to the manufacturer specified maximum service life. Long and short, nothing will replace the need for proper inspection of equipment before use to make sure equipment damaged by environmental exposure or other issues is kept out of service.
Environment can be a helmet’s worst friend
As with webbing and rope, environmental exposure can cause damage to a critical component of PPE, a technician’s safety helmet. Studies are limited, in fact, CSA (Canadian Standards Association) Z94.1-2015 removed UV resistance requirements and pre-conditioning procedure pending future research to validate the procedure against real-life exposure to sunlight.
Still, there are best practices that can extend the life of helmets and ensure proper function.
Temperature extremes can cause internal and external helmet damage. While working in extreme cold the helmet can become brittle and crack. Extreme heat can cause damage to soft lining materials. Additionally, sweat can cause damage to a helmet by degrading the interior lining, causing adhesives to fail and compressing the foam. This makes the helmet fit looser and will cause it to be less effective than a helmet with a proper fit. Prevention is simple, regularly wash the lining if it is removable and make sure it is dried thoroughly and slowly out of direct sunlight. If the lining is not removable, spray the inside with a helmet interior cleaner. Many manufacturers will provide further information on how to clean the helmet and their information should be the default method.
As with the nylon webbing study, UV degradation is one of the most significant problems to monitor. Signs of thermal damage on the outer shell include bubbling, soft spots, warping, and discoloration. Signs of damage can appear on the interior lining. These include charring, burn holes, melting, and loss of seam integrity. To prevent this damage, use a storage hook (where fitted) and store out of direct sunlight, especially behind glass or in vehicles during high summer temperatures. Some technologies do exist to both prevent and warn of UV degradation such as UV resistant gloss and matte paint or indicators that change color based on exposure levels.
To sticker or not to sticker?
Degradation can also be caused by sources outside of environmental exposure: adhesive stickers or paint on protective helmets. It is a contentious topic and common industry practice, but OSHA does provide guidance through a Standard Interpretation. (The full letter is available here). In summary, OSHA Standard 29 CFR 1910.132(a) requires that PPE be, “…maintained in a sanitary and reliable condition…”. To ensure a helmet is and remains in a, “reliable,” condition, the helmet must be inspected prior to each use for signs of dents, cracks, penetration, and any damage due to impact, rough treatment, or wear that might reduce the degree of protection originally provided. Paints and stickers may also eliminate electrical resistance and – depending on the location and quantity – conceal defects, cracks, penetration, and any damage that would otherwise be readily identifiable during the employee’s inspection to ensure reliability. Another concern is that paints, thinners, and solvents can also attack or damage the shell of the helmet and reduce protection.
For these reasons, painting or applying stickers must be performed in accordance with the manufacturer’s instructions unless the employer can demonstrate that the altered protective helmet is equally as effective and protective as those meeting the requirements of Z89.1. OSHA considered painting or placing adhesive stickers acceptable if the manufacturer authorizes the alteration or the employer can demonstrate the reliability of the helmet is not affected by the paint or adhesive on the stickers; and the paint or placement of the stickers does not reduce the ability to identify defects or other conditions that would indicate a reduced reliability.
This standard interpretation serves to further stress the importance of storage and inspection practices. They must be followed to extend the helmet’s service life and protect technicians from a fall, slip, or drop while wearing a compromised helmet. The equipment that is used for work in telecommunications is exposed to many different applications and environments.
AUTHORS’ NOTE: The intent of this PAN is to raise awareness of the environmental issues and to stress what should always be done: the proper inspection of all equipment by a competent person in compliance with a manufacturer’s specifications.