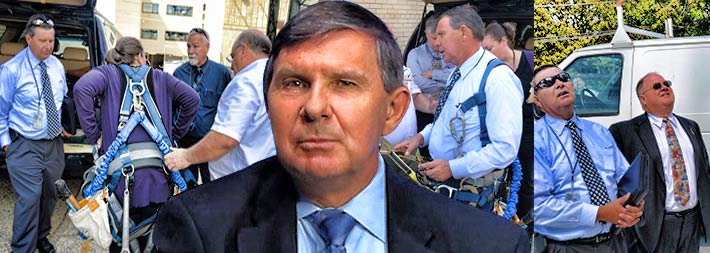
Jim Maddux, one of OSHA’s more approachable directors, took time out during his last few days on the job for a Q&A with Wireless Estimator. He leaves the agency with a record of helping to reduce tower climber deaths.
Jim Maddux, Director of the Occupational Safety and Health Administration Directorate of Construction, retired at the end of December from the position he held since Dec. 20, 2010.
During his leadership at OSHA he was instrumental in creating a serious conversation about climber safety in America, and shepherding new proactive initiatives targeting the telecom industry.
He began his carrer with OSHA in 1990 as a statistician. Maddux held several leadership positions at OSHA, including Director of the Office of Maritime and Acting Deputy Director for the Directorate of Standards and Guidance.
“As I’m closing my career at OSHA and entering into retirement, I have really enjoyed working with the dedicated and caring people in the telecommunication industry,” Maddux said last month.
“I’ve met many fine people, had hundreds of great conversations, and hope people in the industry will continue to strive for a safe and healthy workplace.”
Of a number of inviting comments he provided in a Q&A below with Wireless Estimator, Maddux reflected upon the agency’s ability this year to increase OSHA fines for those larger companies who sometimes consider them as “just another cost of doing business,” noting that “the maximum penalty for illegally copying a movie is $250,000, or twice OSHA’s newly increased authority for penalizing an employer who willfully violated a standard, even if the violation resulted in a fatality or serious injury.”
As a further example, Cumulus Media Inc. agreed yesterday to pay an FCC fine of $540,000 because it didn’t identify the sponsor of an ad it ran.
One of the most difficult rules to get approved during his career, taking more than 10 years, was a standard requiring employers in all industries to not only provide, but also pay for personal protective equipment, Maddux said.
A Q&A with OSHA Director of the Directorate of Construction Jim Maddux
The ability for worker certifications to enhance the industry
Q: Prominent companies and organizations in the wireless industry recently came together to establish the National Wireless Safety Alliance (NWSA) organization. The NWSA is the first national certification organization to be developed for the communication tower industry’s workforce. From your experience with other industries who have a similar organization (ie – the crane industry), how does national worker certification enhance overall worker and industry safety?
A: OSHA’s first experience with using third party certifications in a safety standard was with the crane industry, and we are continuing to work through several issues related to crane operator certification. I think certifications can play an important role in safety, especially by providing a testing mechanism that verifies specific knowledge and abilities. At the same time, it appears that there are limitations on what certification can accomplish. I would not want to see certifications replace worker training, and think there is still a lot to learn about how to use tests to measure safety skills.
OSHA’s active participation in understanding tower work
Q: During your tenure, the Agency became more involved in participating in hands-on activities such as the Industry Leaders Authorized Climber Training Event in 2014 and the NATE Tower Site Tour in 2012. How has OSHA’s active participation at these events helped the Agency in terms of its understanding of the unique challenges that workers face when it comes to tower construction and maintenance activities?
A: I think these types of work are very important to OSHA, and especially to the staff who are doing the hard work to develop workable solutions to difficult issues. We have visited dozens of tower sites and talked to many others about communication tower safety. We continue to learn more about the industry from those conversations and consider them an important part of our efforts.
Creating relationships with NATE and other organizations
Q: Throughout previous administrations, OSHA had a long-standing industry partnership with the National Association of Tower Erectors (NATE) that seemed to be successful from the standpoint of best practices data sharing, promoting safe work practices and incentivizing employer and employee compliance. In 2009, OSHA discontinued the partnership program with NATE and other organizations. What were the benefits of OSHA’s partnership programs to the industry? Given the spotlight on the tower industry, was this a good decision in retrospect to discontinue this partnership program with NATE?
A: Actually, NATE discontinued the partnership because they did not agree with some of the changes that OSHA wanted to make in the partnership agreement. But rather than rehashing those issues, what matters now is that we are currently working closely with NATE and other organizations. We have professional and productive relationships with many people in the industry, and these ties are helping everybody share information and ideas to do the work more safely.
‘Riding the Line’ and worker fatigue
Q: NATE’s Legislative and Regulatory Committee worked closely with you and your colleagues at OSHA to update the compliance directive when it pertains to the “Riding the Line” provision. The CPL Directive was ultimately updated in the summer of 2014 to allow workers to “Ride the Line” under specific conditions for both new construction and general maintenance work on towers. From your perspective, how will this updated CPL 02-01-056 help enhance elevated worker safety and reduce the ongoing repetitive stress that tower climbers endure?
A: We were able to update the directive to make sure that the same work practices were being used during maintenance and construction work, and that will help ensure safer lifting of personnel. It appears that more companies are moving away from lifting personnel with drum hoist devices. While that removes workers from the potentially fatal risks involved in the lifting process, it could contribute to worker fatigue. Worker fatigue is a major safety issue for tower climbers who often travel long distances just to get to the job site, and their employers need to make sure their workers are properly rested and able to do the work safely.
Agency’s relationship with FCC’s safety concerns
Q: The FCC and OSHA recently announced plans to host the 2nd Annual workshop on Tower Climber Safety in February of 2016 in Washington, DC. How has OSHA’s ongoing joint collaboration with the FCC been going when it comes to tower climber safety? What does the Agency hope to accomplish at the 2nd Annual Tower Climber Safety Workshop?
A: We have an ongoing conversation with staff at the FCC and believe it has been a very worthwhile collaboration. We have a lot of issues where we have a common interest, and the FCC’s involvement has brought additional parties into the tower climber safety discussion. We are working with the FCC and the Employment Training Administration to organize the second joint meeting of the agencies, and hope that it will help employers and their workers move forward and create safer workplaces.
Severe Violator Enforcement program as a deterrent
Q: In September of 2014, OSHA placed a wireless contractor on the Agency’s Severe Violator Enforcement Program following the death of two of the company’s workers. Has the program been effective in OSHA’s desire to attack construction safety violators on multiple fronts?
A: The Severe Violator Enforcement Program, or SVEP, has been an effective way to identify and follow up with employers who have the worst enforcement histories. I’ve talked to many employers who either want to make sure they don’t get on the list, or who are trying to get off it. This tells me that the SVEP is having a deterrent effect and is encouraging employers to do a better job of protecting their workers.
Larger OSHA fines and their effect upon safety
Q: With the amendment that was signed into law by President Barack Obama on Nov. 2, 2015, OSHA can now, based upon inflation, issue a maximum penalty, not later than August 1, 2016, of $127,000 from the current $70,000 for a willful violation.
Even though this is an 80% increase, do you believe that it is enough of a deterrent, or should it be more, especially considering that the FCC can issue a Notice of Apparent Liability for $325,000 for indecent language or nudity?
A: We are not yet sure what the exact penalty increase will be, but we are working to implement the new penalty authority in 2016, and believe that it will improve the deterrent effect of our enforcement program. This is especially true for larger companies who sometimes consider OSHA fines as “just another cost of doing business.” We hope the larger maximum penalty authority will encourage more employers to follow the OSHA standards and protect their workers. I’m not sure what the right penalty authority is, but similar to the FCC example you note, the maximum penalty for illegally copying a movie is $250,000, or twice OSHA’s newly increased authority for penalizing an employer who willfully violated a standard, even if the violation resulted in a fatality or serious injury.
Identifying why tower climbing is no longer the “most dangerous job in America”
Q: Based upon the wireless construction industry’s 19 fatalities in 2006 when there were approximately 10,000 tower techs, according to the then-Assistant Secretary of Labor, “Tower climbing remains the most dangerous job in America.”
Since then, based upon the current workforce of approximately 29,000 climbers and 4 fatalities in 2015, the industry has had a marked improvement, and deaths per 100,000 workers are at 14, which will most likely remove the industry out of the top ten fatality professions in 2015.
What influences do you believe were responsible for the lower fatality rate?
A: I think a lot of influences affected the decline in fatalities in 2015, including OSHA’s enforcement activities and efforts by OSHA and the FCC to bring attention to safety issues. It is clear that, at a minimum, these initiatives have helped create a serious conversation about safety in the industry. New efforts on worker training, safe work practices, engineering controls and consensus standards are also big factors. And I think carriers and tower owners are making a difference by improving contractor oversight to ensure safe work at their properties.
New rules consideration for OSHA’s tower industry RFI
Q: OSHA’s Communication Tower Safety Request for Information (RFI) was unique in the history of the Agency in the high level of participation. In your initial review of the RFI, were there some areas of commonality that you believe should be addressed by OSHA? Does it look like there might be rules promulgation based upon the many comments from all sectors and stakeholders in the industry?
A: I think it is too early in the process to predict the requirements and prohibitions that would make sense in a proposed rule, and we are still considering if regulation is necessary. If OSHA decides to go further in the rulemaking process, the information we received in the RFI will be a major contribution to the rulemaking. I’m very pleased with the participation, and the quality of the comments and suggestions.
Identifying new safety practices needed
Q: Is there a particular safety practice related to the wireless industry you would like to see implemented in the future?
A: Yes, there are many practices employers could implement that I believe would improve safety in the industry. One change that could have a major impact is to improve the engineering decisions for equipment placement, tower modification, and tower demolition. Better engineering decisions, combined with clearer instruction to the crews doing the work, would have prevented many of the most horrific incidents we’ve seen in the last few years. I also think many in the industry would benefit from formal safety and health programs. I’ve seen these programs work in many industries, and with employers of all sizes. Many lives could be saved with these systems.
One accomplishment that is most memorable
Q: In all areas of construction, what was the accomplishment that you are most proud of having introduced or guided through that resulted in greater worker safety?
A: I’ve been very fortunate to have worked on many safety and health standards, initiatives and projects at OSHA. The one that I have really enjoyed, and that has had enormous participation is the joint OSHA/NIOSH/CPWR construction fall prevention campaign and fall prevention stand-down. The initiative has reached thousands of employers and millions of workers. I think it has raised awareness of fall fatalities and injuries and the terrible toll they have on workers and their families.
Looking at a controversial, but important safety standard
Q: What was the OSHA standard that was the most difficult for you to get introduced and approved?
A: First, I want to let you know that every OSHA standard that is published is the result of a team effort, and every standard I’ve worked on would not have been published without a lot of people working hard for a long time. None of them is easy. However, I think the most difficult standard for me was the standard requiring employers in all industries to not only provide, but also pay for personal protective equipment. This was a non-technical, yet controversial and important safety issue and our team worked on it for more than 10 years. Publication of this standard was also bittersweet for me. The original project officer became ill, had to take a medical retirement, and later died. I was asked to step in and carry it forward, which I was glad to do.