Installation Information
Self Supporting Towers
The ideal construction environment for erection of a 300’ self supporting tower project, as pictured here, would be to have acres of an asphalted shake out and assembly area, a competitively priced 165-ton hydro crane within shouting distance, and on-site power coupled with no missing materials and two weeks of perfect weather and crew attendance.
Unfortunately, that is not even close to the norm. A self supporting tower is typically purchased to conform to a minimal lease area, with carrier BTS footprints vying for space. In suburban and rural areas, some tower owners are leasing adequate parcels, but to reduce their capital expenditures, are only clearing and fencing smaller compounds until additional tenant leases are signed, passing on the development cost to the carrier. Although cranes are available in most areas, taller tower heights can require the structure to be erected with a gin pole and hoist , a proficiency that not all erection firms may possess.
For larger self supporting towers, manufacturers often provide climbing provisions on each of the tower legs, step bolts being the most common. Since lighting fixtures and antennas may be distributed on any of the three tower legs, it must be practical to access each leg individually. Some designs provide for welded sections in the top 20’ to 80’.
There are multiple manufactured designs, each one having installation or shipping benefits, from tubular, solid and truss-style solid legs to back-to-back angles. When estimating your installation cost, identify whether the design will affect the total number of days budgeted. In example, an inexperienced crew erecting a back-to-back angle structure might take 5% to 10% longer to construct the tower.
Tower plumb variances
An optical illusion oftentimes presents the image that an installed tower was not plumbed correctly. Specifications, however, allow the structure to be slightly out of plumb, but you wouldn’t notice it unless you were to use a transit.
As stated in TIA/EIA-222-F, the horizontal distance between the vertical centerlines at any two elevations shall not exceed .25 percent of the vertical distance between the twoelevations. Using that equation for a 200’ tower, .25 percent of 200’ is .5’ or 6”, allowing the structure to be off 6”. Therefore, a 400’ tower could be out of plumb 12” and a 100’ tower’s tolerance would be 3”.
The average default pricing provided is based upon erecting a self supporting tower contingent upon the entered height and type of tower. Erection pricing includes the installation of:
Prices will vary throughout the country based upon site conditions, crew and crane availability, and the additional work contracted to the erection crew. Grounding and waveguide bridge installation as well as antenna and line installation are not included.
Average crane expenses have been included in the pricing in additon to mobilization of 90 miles from the erection contractor's place of business.
Budgetary Installation Pricing
|
Self Supporting Erection |
In "My Estimator" enter the height of SS tower |
A 2002 OSHA Instruction allows erectors to lift employees on the hoist line to their work stations at any location on a self supporting tower; however, there are strict guidelines that must be followed. Please view Hoisting Erectors .
We recommend that you contact our valued tower erection companies to obtain additional information about their safety compliance, services, capabilities and experience and obtain a project-specific quotation.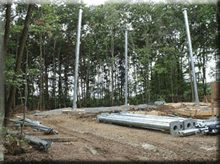
|