Service Information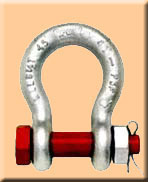
Rigging Equipment
It’s never been officially chronicled, but sometime during the early 1990’s the professional work classification of “Tower Rigger” was eclipsed by “Tower Technician”, some company managers say, because the job requires a greater degree of technical knowledge to construct and maintain communications sites.
However, no matter how many newly acquired skillsets the technican has obtained, rigging knowledge is one of the most essential to ensure a safe installation of structures and equipment. Having safe, fully inspected rigging equipment is vitally as important.
Rigging provides many opportunties for “weakest link” failures from exceeding working loads on shackles and slings to using undersized wire or synthetic rope. Experienced riggers have obtained a wealth of knowledge over the years through training and studying why rigging accidents occur. The truly professional erector will always have ready access to his dog-earred rigger’s handbook to consult it for safe working loads and lifting procedures.
Wire rope slings are rugged and cost efficient, however, synthetic slings have become increasingly popular due to their durable, lightweight and flexible characteristics.
All slings of a web type fabric, nylon or other synthetic material should be labeled to indicate their load rating capacity. They should not be used in a manner that would allow the sling to be cut. Nylon slings available for construction are:
- A. Type 1: These slings have a triangle and choker fitting on either end. They are used in a vertical, choker or basket hitch.
- B. Type 2: These slings have a triangle fitting on each end. They are used in a vertical or basket hitch.
- C. Type 5: The endless sling is the most versatile of all nylon sling configurations. It can be used in a vertical, choker or basket hitch and the wear points can be adjusted around the circumference of the sling to increase its useful life.
- D. Type 6: A reversed eye sling is an endless sling with the edges butted together to double the sling width.
- E. Type 3: A flat eye sling can be used in vertical, choker and basket hitches.
- F. Type 4: Twisted eye slings are similar to flat eye slings except the eyes are twisted 90 degrees to form a better choker hitch and they will nest well in a crane hook.
The same sling will have a different capacity for each hitch. The choker has the lowest capacity. The vertical hitch has an additional 25% capacity and the basket hitch is twice the vertical hitch capacity. The horizontal degree of a two-point pick will affect the load capacity of your sling
Avoid shock loading to nylon or wire rope slings when beginning your lift. The crane or hoist should be engaged slowly until the load is suspended. The speed in which you lift or lower the load should be increased or decreased gradually. Sudden starts or stops place a heavy load on the slings and load line, up to 50 times the actual weight. Once any sling has been shock loaded it must be removed from service.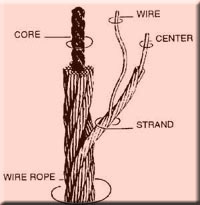
Wire Rope
Manufacturers identify their classes of wire ropes beginning with two numbers such as 6x25. The "6" means that there are 6 strands or larger wires making up the wire rope and the second number "25" means that there are 25 smaller wires laid around each other to make up each strand. The other wires in some wire ropes are called filler wire. Wire fatigue resistance will increase as the number of wires per strand increases.
The 6x19 Seale’s outer wires are larger and provide better resistance to abrasion or crushing on the drum. Outer wires of the 6x21 Filler Wire are larger and fewer than the 6x25 Filler Wire and offer better resistance to abrasion, but slightly less resistance to bending fatigue.
Known as the industry workhorse of wire ropes, the 6x25 Filler Wire maintains a good balance between resistance to abrasion and fatigue resistance. When both abrasion resistance and fatigue resistance are required, the 6x26 Warrington Seale is a better alternative.
A daily inspection of wire rope should be made by passing the cable through gloved hands, flexing it every few inches to expose breaks. Put the rope out of service if there are six or more randomly distributed broken wires in one lay or three or more broken wires in one strand in one lay. Some areas of the wire rope such as around the core are more difficult to inspect. To inspect the core, inspect the rope as it passes over the sheave. The strands have a tendency to open up slightly which will afford a better view of the core.
Keep the wire rope lubricated so that rust and dirt will not weaken it by acting as an abrasive on the rope as it spools through the sheaves and drums. Lubrication of the rope allows individual wires to move and work together so that all the wires carry the load instead of just a few. Weather and other exposures can also remove the lubricant and allow rust to form. When inspecting wire rope, first clean the rope using a wire brush, solvent or steam cleaner. Then, inspect the entire rope for damage in accordance with OSHA 1926.550. Lubricate it well with a lubricant that is thin enough to penetrate all the way to the core but thick enough to coat each wire individually.
Synthetic ropes
Natural and synthetic fiber rope offerings have expanded over the past years with the introduction of new materials such as Kevlar and other advancements that can provide a higher strength and a better abrasion resistant product. A 12-strand ½” rope, provided by one manufacturer identifies a minimum strength of 12,500 pounds, whereas a ½” Kermantle rope is listed as having a tensile strength of 9,954 pounds. A ½” 3-strand polypropylene rope detailed a breaking strength of 4,200 pounds.
Recommended working loads will vary according to the rope size, type and manufacturer. Twisted rope is oftentimes has the working load listed between 10% to 15% of the tensile strength and braided rope is between 15% to 20%. Therefore, a braided rope with a listed tensile strength of 12,500 pounds might only have a safe working load of 1,850 pounds. Ropes have different qualities and you should carefully assess your rigging requirements. In example, Kevlar has a considerably higher breaking strength than most available products, but it fairs poorly if there is a shock load.
It is necessary to check with your cordage vendor to obtain the safe working load of your rope prior to purchasing it for any rigging or lifting purpose!
The working load is the maximum mass or force which any rigging product is authorized to support in general service when the pull is applied in-line, unless noted otherwise, with respect to the center line of the product. This term is used interchangeably with the following terms: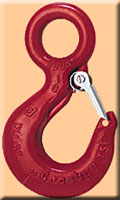
- WLL
- Rated Load Value
- SWL
- Safe Working Load
- Resultant Safe Working Load
A static load is a load resulting from a constantly applied force or load.
Many factors, including rope usage, load conditions and weather exposure affect the rope’s working load capabilities. You should inspect your rope daily for concentrated wear. It must be free of frayed strands and broken yarns, cuts and abrasions, burns and discoloration. If there is excessive soiling or paint buildup, place it out of service. Check for chemical or heat damage and ultraviolet deterioration. This type of degradation is indicated by discoloration and the presence of splinters and slivers on the rope surface. Do not use wire rope or V-belt sheaves for synthetic rope as the rope will be pinched inside.
Basic requirements for rigging safety can be found in OSHA standard: 29 CFR 1926.250-251, subpart H. By following the recommendations by manufacturers and being in compliance with ANSI/ASME standards you’ll provide a safe working environment.
Pricing for rigging equipment is product and load capacity specific.A 1000’ reel of ½” 6x25 wire rope with a breaking strength of 23,000 pounds will average $1,350.00 . A ¾” wire rope with a breaking strength of 51,200 pounds will be $2,700.00 for 1000’. Add freight and taxes. A ½” double braided rope having a 9,800 pound tensile strength averages $600.00 for 1000’. A 5/8” rope with a tensile strength of 15,600 pounds is $1,100.00 for 1,000’. Expert advice and training should be sought when choosing any rigging equipment or performing any rigging services.
We recommend that you contact our rigging supply companies to obtain additional information about their products and services.
Many of our viewers have requested information about knot tying for rigging. Instead of duplicating the wealth of information that is already available, it's easier to purchase one of the rigging books that are available or visit www.animatedknots.com . It provides a wealth of information with animated features and is oftentimes used by tower crews for training.
|