NIOSH Fatality Assessment and Control Evaluation (FACE) Program
Tower Painter Dies and a Second Painter Injured After Falling
900 Feet While Inside a Man Basket in South Carolina
|
NIOSH In-House FACE Report |
FACE 98-21
|
SUMMARY (top)
A 29-year-old tower painter (the victim) died, and his 16-year-old co-worker was seriously injured when, due to a winch failure, they slid 900 feet down a guy wire while in a man basket, striking the base of a guy wire anchor. The workers were painting the sixth highest of nine guy wires on one side of a 2,000-foot television broadcast tower. The victim and co-worker entered the man basket at the guy wire ground anchor, ¼ mile from the tower, and were raised to the sixth guy wire. The owner was operating the winch ¼ mile away from the opposite side of the tower. As the workers were preparing to paint, the basket suddenly jerked then began to slide backward down the guy wire. As the basket began to accelerate, the victim radioed the owner to stop the basket. The owner pulled as hard as he could on the handbrake lever. When that failed to slow the winch’s cable spool, the owner tried to jam a wooden handle into the winch’s gearbox. This action caused the components inside the gearbox to shatter as the man basket continued to slide backward down the guy wire. The victim told his co-worker to lie down on the basket’s floor, then the victim lay down on top of the co-worker. The basket fell until it struck the base of the guy wire anchor. The victim was thrown from the basket and wedged between two hairpins anchoring the guy wire. The injured co-worker unhooked his lanyard and crawled from the man basket. When the basket disappeared from view behind the trees, the groundsman got into his truck and drove to the guy wire anchor point. He placed the injured co-worker in the truck and drove him back to the tower. The owner summoned the emergency medical service (EMS) from a cellular phone, then stayed with the injured co-worker while the groundsman returned to the victim. When the EMS arrived they removed the victim from between the hairpins and summoned the county coroner, who pronounced the victim dead at the scene. The co-worker was transported to the local hospital where he was treated. NIOSH investigators concluded that, to prevent similar deaths and injuries, employers should:
-
ensure that hoisting equipment used to lift personnel is designed to prevent uncontrolled descent and rated for these purposes
-
maintain and inspect hoists according to manufacturers’ specifications to ensure proper functioning
-
know and comply with child labor laws which include prohibitions against work by youth less than 18 years of age in occupations which are declared by the Secretary of Labor to be particularly hazardous (Hazardous Orders)
-
develop, implement, and enforce a comprehensive written safety program.
Additionally, manufacturers of guy wire material should:
INTRODUCTION (top)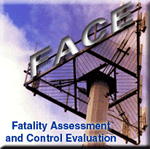
On June 23, 1998, a male 29-year-old tower painter (the victim) died and his 16-year-old male co-worker was seriously injured when they fell 900 feet while in a man basket, striking the base of a guy wire anchor. On July 9, 1998, officials of the South Carolina Occupational Safety and Health Administration (SCOSHA) notified the Division of Safety Research of this incident, and requested technical assistance. On September 23-24, 1998, a DSR occupational safety and health specialist conducted an investigation of the incident. The incident was reviewed with the SCOSHA compliance officer assigned to the case, the company owner, the owner of the crane service inspecting the hoist’s gear box, and the county sheriff and coroner offices. The site was visited and photographed during the investigation.
The company was an out-of-state tower painting service that had been in operation for 3 years. The company owner, the only permanent employee, hired workers as needed to perform contracted jobs. The company had no written safety policy or safety program. Training was performed on the job. The victim had worked for the company for about 2 months. Although the injured worker had been on the job only 2 days, he had worked for the company on previous occasions where working at heights was required.
INVESTIGATION (top)
The company had been contracted by the tower owner to paint the guy wires on a 2,000-foot-high television broadcast tower. The tower was guyed on three sides. Nine, 1¼-inch-diameter guy wires were present on each side. A crew of four workers (company owner, two painters, and a groundsman) were performing the work and had finished five wires on each side of the tower. With the exception of one of the painters who had been on site 2 days, the crew had been at the site 1½ weeks.
On the day of the incident, the victim rode the tower’s elevator to the sixth guy wire from the ground, approximately 1,200 feet above ground, and rigged pulleys on the tower. The winch cable was then run through the pulleys and attached to a 4-foot-wide by 5-foot-long steel man basket that had been fabricated by the company owner. It was standard operating procedure for the victim to rig and test the pulleys and cables before lifting personnel. The man basket was attached to the guy wires by two steel collars which were welded to the top right rail of the man basket and were clamped around the guy wires. The winch cable was attached to the upper left rail of the man basket, allowing the basket to remain level while the men were inside (Figure 1).
Once the rigging was complete, the victim rode the elevator to the ground, loaded the paint and supplies on the elevator, then took them up to the level of the sixth guy wire. He then returned to the ground and was transported along with the other painter to the guy wire anchor by the groundsman. The victim rode the man basket up the guy wire, and loaded the paint and supplies in the man basket. The company owner was operating the winch, which was located approximately ¼ mile from the tower (Figure 2). The guy wire anchor for the wire the workers were painting was located approximately ¼ mile on the opposite side of the tower, or ½ mile from the winch. Due to a line of trees, the company owner could not see the workers in the basket from his location, but maintained contact with the two workers in the man basket via two-way radios.
Once the man basket was loaded, the victim returned to the ground to pick up the co-worker. The two men then rode the man basket to the 1,200-foot level and began painting. The victim was not wearing fall protection, the second painter was wearing a safety belt and a lanyard that was attached to the manbasket. Shortly after noon, the men had painted down the guy wire to the 1,000-foot level. The victim radioed the company owner to lower the man basket a short distance. As the basket stopped, it suddenly jerked. The co-worker asked the victim what had happened, and the victim said he did not know. The basket then began to drift backward down the guy wire. The victim called to the company owner and asked what was wrong. As the man basket reached the 900-foot level the basket began to pick up speed. At that point, the owner pulled as hard as he could on the handbrake lever. When that failed to slow the winch’s cable spool, the owner tried to jam a wooden handle into the winch’s gearbox. When he did so, the components inside the gearbox shattered, allowing the man basket to free fall. The victim told his co-worker to lie down on the basket’s floor. The victim then lay on top of the co-worker. The basket fell until it struck the base of the guy wire anchor. The victim, not wearing fall protection, was thrown from the man basket and wedged between two hairpins anchoring the guy wire (Figure 3). The co-worker unhooked his lanyard and crawled from the man basket. When the basket disappeared from view behind the line of trees, the groundsman got into his truck and drove to the guy wire anchor point. He placed the injured co-worker in the truck and drove him back to the tower. The owner summoned the emergency medical service (EMS) from a cellular phone, then stayed with the injured co-worker while the groundsman returned to the victim. When the EMS arrived they removed the victim from between the hairpins with the help of sheriff’s deputies and summoned the county coroner, who pronounced the victim dead at the scene. The co-worker was transported to the local hospital with multiple fractures where he underwent surgery.
Investigation revealed that the winch was purchased by the owner used when he started the company 3 years ago. The winch was manufactured for use on oil drilling rigs and was not rated for hoisting personnel. No service records were kept by the owner who stated that he never had the winch inspected, although he changed the oil periodically.
When the components in the gearbox shattered, the cover of the gear box and a universal joint were thrown 40 feet from the winch. The winch was taken to a hoist and winch service shop for inspection, and it was found that the gears inside the gear box were all stripped. Although the brakes were broken as a result of the incident, it could be seen that they had been worn.
CAUSE OF DEATH (top)
The county coroner listed the cause of death as massive trauma.
RECOMMENDATIONS/DISCUSSION (top)
Recommendation #1: Employers should ensure that hoisting equipment used to lift personnel is designed to prevent uncontrolled descent and is rated for these purposes.
Discussion: The hoist used in this incident was not rated for the transport of personnel, and warning labels on the hoist stated that the winches were not intended for use in the lifting or moving of persons. The hoist was manufactured for use on oil rigs. Equipment should only be used as rated by the manufacturer in accordance with 29 CFR 1926.553 (a)(4) which states all base-mounted drum hoists in use shall meet the applicable requirements for design, construction, installation, testing, inspection, maintenance, and operations, as prescribed by the manufacturer. OSHA CPL2-1.29 requires that hoists used to lift personnel must be designed to use power lowering. The hoist in this incident was designed for friction lowering, or using the gearing and handbrake to lower the man basket. Additionally, CPL 2-2.19 requires that hoists used to lift personnel be equipped with a primary brake connected directly to the drive train of the hoisting machine and a secondary automatic emergency-type brake that, if actuated, would be able to hold the rated load within a vertical distance of 24 inches. The hoist involved in this incident was equipped with neither type brake.
Recommendation #2: Employers should maintain and inspect hoists according to manufacturers’ specifications to ensure proper functioning.
Discussion: The employer in this incident had no documented maintenance records for the hoist and had never done a comprehensive inspection of the hoist. The hoist involved in the incident was not rated for personnel lifts; however, all hoists should be maintained according to manufacturers’ specifications.
Additionally, all hoists should be inspected as outlined in the OSHA interim guidelines for employee access by hoist during communication tower construction activities. These guidelines state that all hoists should undergo routine inspections. All hoists shall be visually inspected by a qualified person each day before use. All hoists shall also be inspected thoroughly at 3-month intervals by a qualified person, as will any hoists that have been idle for more than 1 month but less than 6 months. Such inspections will include a hands-on operation of all moving parts to ensure that they are intact and will properly function before being put into service. All hoists shall also undergo a tear-down inspection annually unless the following conditions exist that allow for less frequent tear-down inspections:
(1) A hoist that has been idle for a period of over 6 months shall be given an annual inspection which should include the hoist being completely disassembled, cleaned and inspected. Parts such as pins, bearings, shafts, gears, brake plates, etc. found worn, cracked, corroded, distorted or otherwise non-functional must be replaced before the hoist is used.
(2) Hoists with infrequent to moderate usage (hoists that have been used for 50 hours or less per month and normally operate at considerably less than the hoist rated capacity based on the average use over a month) may go up to 36 months between tear-down inspections if serviced under a preventive maintenance program (as specified by the manufacturer) that includes annual hydraulic oil sample analysis. An oil sample analysis, meaning a laboratory analysis, is used to evaluate the mechanical integrity of the hoist. Oil in these hoists shall be changed at least on an annual basis, just after the oil analysis is performed. Hoists not subjected to recommended oil sample analysis shall undergo an annual tear-down inspection.
(3) Hoists that experience heavy usage (hoists that are used for more than 50 hours per month) may go up to 24 months between tear-down inspections if serviced under a preventive maintenance program as outlined in (2) above.
(4) Any rebuilt hoist assembly must be line pull tested to the rated load. The hoist drum must be rotated several times in both raising and lowering directions under full-rated load, while checking for smooth operation.
Recommendation #3: Employers should know and comply with child labor laws which include prohibitions against work by youths less than 18 years of age in occupations which are declared by the Secretary of Labor to be particularly hazardous (Hazardous Orders).
Discussion: The Fair Labor Standards Act provides a minimum age of 18 years for work which the Secretary of Labor declares to be particularly hazardous (Hazardous Orders). One of the 17 Hazardous Orders prohibits minors from work in all occupations where work involves riding on a manlift (Hazardous Order No. 7). The term manlift shall mean a device intended for the conveyance of persons which consists of platforms or brackets mounted on, or attached to, an endless belt, cable, chain, or similar method of suspension; such belt, cable, or chain operating in a substantially vertical direction and being supported by and driven through pulleys, sheaves or sprockets at the top and bottom.
Recommendation #4: Employers should develop, implement, and enforce a comprehensive written safety program.
Discussion: The employer had no written safety program, safety policy, or safe work procedures. The development, implementation, and enforcement of a comprehensive safety program should identify and reduce or eliminate worker exposures to hazardous situations. The safety program should include, but not be limited to, employing worksite hazard assessments to enable the recognition and avoidance of fall hazards; and providing, and enforcing, the use of appropriate safety equipment such as safety nets or safety harnesses and lanyards. Additionally, the safety program should outline procedures and schedules for the proper maintenance of equipment and machinery and provide for the documentation of such maintenance.
Recommendation # 5: Manufacturers of guy wire material should continue research and development of materials that would not require periodic painting.
Discussion: Guy wires require tremendous tensile strength. In this case, they were torque to 100,000 pounds of tension. Because of these requirements, only certain materials can be used. At this time the materials that can be used require periodic painting to protect and maintain the integrity of the materials. Manufacturers of guy wire materials should continue the research and development of materials that would not require periodic painting to protect the materials.
REFERENCES (top)
Code of Federal Regulations 29 CFR 1926.553 (a)(4), 1997 edition. U.S. Government Printing Office, Office of the Federal Register, Washington, D.C.
CPL. 2-1.29, Compliance Directive for Employee Access by Hoist During Communication Tower Construction Activities [1999]. United States Department of Labor, Occupational Safety and Health Administration, Washington, D.C.
DOL (1990). Child labor requirements in nonagricultural occupations under the Fair Labor Standards Act. Washington, D.C.: U.S. Department of Labor, Employment Standards Administration, Wage and Hour Division, WH 1330.
|