Installation Information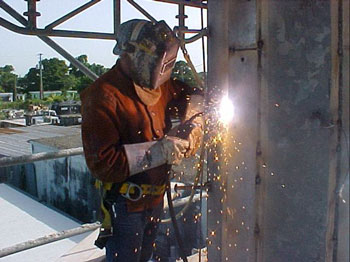
Elevated and Ground Welding
The increasing demand for tower co-locations has brought welding to the forefront of the communications construction industry. Numerous engineering groups are proposing welded solutions to strengthen towers and monopoles. On some occasions, water towers are getting reinforcements as well. Welding additional steel on tower legs and bracing is one of the most effective ways to increase the structure's capacity, easily allowing for excess load transfer and ensuring that steel members will not buckle. This low profile process adds very little wind load to an already loaded tower.
Depending upon the type of structure and height, sometimes engineers will design a bolt-on system when they believe welding could contribute to a catastrophic accident. Although they know that they can provide a safe retrofitting design, they're concerned about their liability since they oftentimes have no oversight of the client's contractor and their capabilities. They're also aware that the owner's low-bid selection may not provide the experienced welders and installers that the project will require.
Selecting a qualified contractor to perform this work is extremely important. A contractor with intimate metal knowledge will take the precautions to protect both the parent structure and the property on which it is located. It's imperative to ensure that the contractor has fully trained certified welders. A contracting company attempting to perform work outside their normal scope will most likely be unaware of all hazards that welding presents when working at high elevations. For additional information about the types of welding, equipment and consumables, see Welding Equipment and Supplies.
Extensive fire safety precautions required
A senior hazard of welding is fire. Numerous towers have been damaged or destroyed. While contractors were welding on a 520’ multi-carrier tower in Naples Florida during July of 2004, a resulting fire at a lower level caused the legs to buckle, collapsing the structure, just moments after three welders climbed down the tower. Coverage from multiple carriers was non-existent for almost a week following the incident until a portable cell site could be brought in and assembled.
Recent tower fires have resulted in a few owners requesting “low heat welding” to reduce the risks. However, there aren’t any standards for procedures that offer low heat. The American Welding Society does not define processes as high heat or low heat as provided for in some specifications. A specific process must be selected as suited to its need and intended use. A non-standard procedure will need to be proven and qualified in most situations because of material quality.
An extensive fire safety check should always be performed as the site conditions change as the elevation of the welding increases. All debris as well as dried grass and dead vegetation should be removed. If you find a bird’s nest on the tower or inside the monopole, have your client contact the appropriate authorities to ensure that it can be removed. Also, you may be required by some owners or carriers to flush the inside of monopoles with water while cutting monopole sections to extinguish hot airborne material.
Where applicable, a dampened plywood covering should be placed over waveguide bridges and other areas that need protection against fire. It is advisable to install a fire blanket around coax cables in the cutting area of the structure and keep the blanket saturated with water.
Transmission line jackets, when ignited, can cause high heat that can weaken and collapse the structure. Some structures have been damaged when welding ignited cluster blocks, wicking the flames to the coaxial lines.
The proper types of fire extinguishers should be available for each type of fire that may result; a fire plan and assignment of tasks should also be included during on-site safety meetings.
Review specifications and tower owner’s prohibitions
Review the tower owner’s welding requirements prior to bidding upon any project to ensure that you have priced the welding correctly and are not in violation of any client restrictions. Some owners will only allow one welder to weld on the structure at any one time. Also, a dedicated employee must be on site at all times watching the project from a suitable viewing area to extinguish potential fires.
Most contract specifications require the welder to be AWS D1.1 qualified and be familiar with ANSI Z49.1 “Safety in Welding, Cutting, and Allied Processes”.
The American Welding Society regulation AWS D1.1 is the code specified on almost every drawing produced by design engineers. It has specific guidelines as to what qualified welding process should be used for the materials being welded and how to qualify a welding procedure. If you are bidding a modification requiring welding, you should be familiar with AWS requirements to ensure that your welders or subcontractors are in compliance as required by the engineer’s general notes.
Using oxy-fuel gas or plasma cutting on tower structures is oftentimes prohibited. Reciprocation saws and metal cutting circular saws/grinders with carbide blade/disc and depth gauge are recommended for cutting structural steel.
Pricing is always project specific. We recommend that you contact our listed welding professionals to obtain additional information about their services, capabilities, experience and pricing.
Respirator fitting a must
Welding on towers also presents a danger to employees, as the smoke produced is poisonous. This smoke however, can be overcome with simple and affordable breathing apparatuses. Fitting an employee to his or her own respirator is strongly recommended and in some cases mandatory. The fitting process will insure that a respirator matches the breath volume (amount of air intake and exhaust in one breath) to that of the employee. Sharing of respirators is not recommended and is illegal in some work situations.
When welding on towers the integrity of the parent metal is of great importance, and is most commonly the first item to suffer from welding by persons not qualified to perform the work. The proper weld procedure for the type and quality of material to be welded must be followed in order to get the desired quality of weld and protect the overall integrity of the project.
Proper pre-heating and weld deposition rates must be achieved to insure that heat affected zones and weld areas are in compliance with the weld as designed by the engineer. Weld procedures have many variables. Proper use and control of these variables work as the formula to achieve proper penetration, fusion, weld deposition and weld size.
There are pre-qualified procedures for the 50 KSI and 65 KSI materials used in towers; those that are written are very strict and are oftentimes not performed properly by some contractors. AWS pre-approved or pre-qualified procedures for these materials require a weld on a vertical axis to be performed in a vertical up progression, meaning that the tower welder should begin the weld pool at the member’s lowest point and travel in a vertical up direction to deposit the weld material.
After the welding has taken place, restoration of the affected galvanizing should be done. Use of an appropriate coating and its application procedure are mandatory. An improper coating will result in early deterioration. Several types of coatings are available from as many manufacturers. Research the product you wish to use and be sure it meets the requirements of the geography where it is to be used. Extreme cold or ice found in mountainous climates will affect a paint coating very differently than salt breezes found near the ocean. High temperatures will also be factors in choosing a coating.
|