Product Information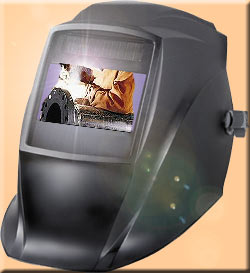
Welding Equipment/Supplies
Oxy-fuel welding another 20’ section onto a foundation tremie pipe, arc welding a reinforcing collar on a structural retrofitting project and plasma cutting an additional port hole on a rooftop enclosure are just a few of the dozens of daily cutting and welding procedures in wireless construction, in addition to the many welding requirements necessary to maintain the contractor’s equipment.
Equipment selection is based upon the fabrication requirements such as the type and thickness of the weld as well as mobility needs.
Oxy-acetylene welding or cleaner and hotter oxy-propane welding is extremely versatile and is the only gas flame that is hot enough to melt all commercial metals. It’s simple in concept. These processes, used with or without the application of filler in the weld pool, produce coalescence in the work pieces by heating them with an oxy-fuel gas flame. The weld lines, however, require more finishing and the heat affected zones can adversely affect the metals mechanical properties.
SMAW (Shielded Metal Arc Welding), commonly called stick welding, is the most common form of arc welding in wireless construction because of the versatile applications for field work. SMAW is an arc welding process with an arc between the weld pool and a covered electrode. As the decomposition of the electrode occurs, electrode metal becomes the filler metal while the covering provides the shielding of the weld pool. The electrode (welding rod) diameters most commonly used are 3/32”, 1/8” and 5/32”. By heating the coated stick electrode and the base metal with an arc, a fusion of the metal is created. The heat is created by an AC or DC electrical current. Engine-driven welders are typically used when electric power is not available and are excellent for field construction; however, they are also used indoors when it is not convenient for plug-in arc welders or if the equipment’s load requirement is not available. Low hydrogen fillers should be used on steel used for tower fabrication.
Many contractors are now using FCAW (Flux Cored Arc Welding) procedures to increase production and lower their labor costs.
Gasoline powered engines are typically less in price and are preferred in colder climates, but they have less fuel economy than a diesel model. When exhaust emissions are not allowed for indoor applications, liquid propane gas models can be purchased. A unit that delivers 250 amps of AC or DC weld power is more than adequate for most wireless construction projects.
Capacitor discharge stud welding is a semi-automatic arc welding process. The CDSW process operates on the principle of capacitor stored energy, which is instantaneously discharged by the equipment system through a special weld “timing” tip. Since the entire weld cycle is completed in several milliseconds, properly created welds can be made to steel without distortion, burn-through or discoloration. Capacitor discharge welding permits stud welding of dissimilar metals. A stud gun with spring pressure holds the stud against the intended work. Stored energy is discharged and the stud starts downward. The stud is then forced into molten metal which solidifies and the weld is completed in a split second.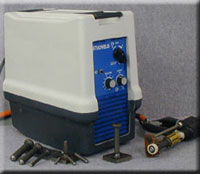
Arc stud welding is a welding process where the gun solenoid lifts the stud from the metal surface and creates an arc which melts a flux-loaded end of the stud and its immediate area. A ceramic ferrule shields the arc, concentrates the heat and contains the molten metal in the weld zone. Simultaneously, the gun solenoid becomes de-energized and the spring tension forces the fastener into the molten pool, integrating it with the parent metal. The expendable ferrule is then broken away to expose a smooth and complete fillet at the stud base.
Plasma cutters create a constricted cutting arc which easily slices through metals. A high velocity jet of ionized gas removes molten material from the application. This process can be used to cut both ferrous and non-ferrous metals.
Welding helmets are one of the most important safety accessories in welding. They should filter out 100 percent of the harmful ultraviolet (UV) and infrared (IR) wavelengths. The lens shade number is oftentimes mistaken for the protection that is provided; it is only a guide for selecting the lens that is most comfortable for the user while providing good visibility.
High quality auto darkening helmets have a response time of 4/10th of a millisecond. Since the eye can’t perceive anything less than a millisecond, the initial arc strike will not cause any discomfort.
For additional welding information, see Elevated and Ground Welding.
Welding equipment supplies and consumables are available on line from many distributors. Some of them provide excellent resources and pricing. However, many contractors prefer suppliers that have the personnel readily available to discuss their equipment fabrication requirements. Good oxy-acetylene welding outfits will cost $300.00 plus the cost of the oxygen and acetylene tanks. A 10,000 watts, 250 amps gasoline welding generator averages $2,900.00. A 3/8” air plasma cutting system averages $1,000.00; a 1” cutting system costs $2,500.00. Welding helmets are available from a basic fixed front for $25.00 to an auto darkening solar powered unit for $325.00. Some manufacturers provide designer helmets costing as much as $495.00. For tower accessories manufacturers, robotic systems are available starting at $55,000.00.
We recommend that you contact our valued welding equipment manufacturers and distributors to obtain additional information about equipment, accessories and consumables.
|